Big Data is changing the face of manufacturing as we know it. Gone are the days when data scientists needed to mine, organize, and manage volumes of diverse data manually or run experiments to test the hypothesis. With enterprise Big Data solutions, manufacturers can predict business outcomes, enhance the quality of their products, reduce equipment downtime, and optimize costs.
More and more manufacturers are adopting Big Data at their plants. As the adoption grows, so does its market size. According to Fortune Business Insights, the Big Data market in the manufacturing industry is predicted to reach $9.11B by 2026. So, your business should be ready for the era of Big Data, too.
Why is Big Data crucial for manufacturing software? How is Big Data changing the world of manufacturing? How to take full advantage of Big Data in manufacturing? We’ve tried to answer these and a few other questions.
Why do manufacturers need Big Data?
Big Data in manufacturing offers many benefits, including lower operating costs, greater production efficiency, and improved risk management.
Leading manufacturers use Big Data to analyze the flow of finished goods and respond better to demand signals. IBM states that 53% of manufacturers apply Big Data and Data Analytics to create a competitive advantage for their organizations [2].
Big Data in the manufacturing industry helps to rationalize processes and thus eliminate unnecessary expenses. For example, with the help of Big Data, John Deere (Deere & Company) saved $900M in inventory control over two years. Also, the Coca-Cola Company saved around $45M annually by following Big Data analysis [6].
Now, let’s analyze the benefits of Big Data implementation in more detail.
Benefits of Big Data in manufacturing
1. Reduced machine downtime
Big Data is used for predictive and preventive maintenance to reduce hardware downtime, one of the most common issues in manufacturing. Hardware downtime requires immediate troubleshooting from engineers, which slows down the whole manufacturing process. Thanks to Big Data, manufacturers can predict machine failures and take proactive measures to repair the equipment and ensure that production doesn't reach a standstill. What’s more, some modern technologies allow self-diagnostics and can automatically shut down to prevent further damage.
Big Data analyzes vast amounts of information. It helps recognize patterns in the data, thus predicting when the machine may fail. Thus, fixing the problem and reducing operational expenses by up to 50% is easier [5].
Equipment breakdowns and scheduled maintenance are part of the game in manufacturing. However, Big Data analytics can reduce the time required for these activities. Forbes states that Big Data in the manufacturing industry can reduce breakdowns by 26% and unscheduled downtime by 23% [5].
2. Enterprise growth
Big Data tools help compare the performance of different sites and pinpoint the reasons for the differences. With Big Data, you can analyze your production plants, develop what-if scenarios, and apply predictive models. Based on factual data gained through Big Data analysis, you can make a well-informed decision about where to open a new factory, which company site should be relocated/closed, whether to introduce a new product, etc.
3. Better cost management
Predictive analytics make budget planning easier. It is now possible to understand the costs needed for problem-solving.
Also, Big Data analytics can help to track and understand the root causes behind overhead costs. Manufacturing businesses can’t start reducing their indirect costs without knowing the average amount they spend on things each month. Big data analysis helps in this area by providing baselines that inform manufacturers of their most substantial indirect expenses. Then, it is possible to start figuring out where to make improvements.
Learn more about cost reduction in the manufacturing industry
4. Enhanced customer service
The success of your manufacturing business depends heavily on the satisfaction of your customers. With Big Data, you can analyze their experience with your product, thus making it better. Deloitte claims that 36% of consumers are interested in purchasing customized products and services, and 48% are ready to wait longer for those goods. So, Big Data and IoT in manufacturing can provide valuable insights into your customer experience.
Big Data in manufacturing is no longer a choice; it is a must that helps to stay competitive in the vast manufacturing market. Forward-thinking manufacturers leverage advanced analytics to unlock actionable insights, optimize operations, and achieve industry-leading performance. Now, let’s examine several trends that are prevailing now.
Trends of Big Data in the manufacturing industry
#1 The hybrid and multi-cloud data strategy
The market is moving to interoperable multi-cloud environments with the ability to connect private and public clouds. The hybrid and multi-cloud approaches allow companies to gain visibility and control over all the places where they’re doing business. Thus, manufacturing can introduce innovations in a much more secure and efficient manner.
Two main reasons manufacturers opt for the hybrid and multi-cloud data strategy are cost optimization and security. Manufacturing businesses choose to store their data in a hybrid cloud to control their cloud expenses. According to Flexera, over 36% of manufacturers that use just public cloud state that their cloud spending exceeds their budget.
Moreover, hybrid cloud and multi-cloud strategies are touted as secure data storage methods, and 34% of manufacturers choose security and compliance as their top priority. So, we expect to see later adopters of Big Data bring the hybrid and multi-cloud methodology to the forefront of data ecosystem strategies.
Read more about cloud computing in manufacturing
#2 A Data hub
While data lakes and warehouses have been valuable in capturing and storing vast amounts of manufacturing data, the industry is shifting towards a more sophisticated approach: data hubs. A data hub is a centralized platform for integrating and organizing data from diverse sources, including traditional data lakes. This structured environment allows manufacturers to store raw data and refine it into a usable format for advanced analytics.
Data hubs excel at addressing the dynamic nature of manufacturing data, providing agile solutions for data ingestion and transformation. This flexibility ensures manufacturers can easily adapt to evolving data requirements and industry standards.
Cost-effectiveness is a key advantage of data hubs, which leverage scalable infrastructure and storage solutions to optimize resource utilization. Whether processing data in real-time or batches, manufacturers benefit from efficient data management practices that drive operational efficiency and cost savings.
Moreover, data hubs enable predictive analytics within the manufacturing sector. Refined data within the hub facilitates advanced analytics, leading to more accurate predictions for predictive maintenance and optimized production processes.
#3 Machine Learning and AI
Machine Learning and AI use in data-driven organizations is not limited to merely fixing existing failures. Big Data, Machine Learning, and AI can recognize patterns in vast amounts of data, thus helping with everything from maintenance to production optimization.
Predictive maintenance 2.0
AI and ML algorithms analyze sensor data, historical trends, and external factors to predict not only when equipment will fail but also the root cause of the issue. This allows for proactive maintenance, minimizing downtime, and optimizing parts replacement schedules.
Process optimization and quality control
AI and ML analyze production data in real-time to identify inefficiencies and bottlenecks. This allows manufacturers to fine-tune processes, reduce waste, and ensure consistent product quality. Imagine AI-powered systems automatically adjusting machine settings for optimal output or identifying potential defects before they reach the final product stage.
Advanced robotics
Collaborative robots, or "cobots," equipped with AI capabilities, can work safely alongside human workers, performing repetitive, hazardous, or high-precision tasks. Unlike traditional robots requiring specialized programming skills, cobots can be programmed through intuitive interfaces, allowing faster deployment and integration into existing workflows.
Alongside the described utilization of AI in manufacturing, there is even greater potential to unlock entirely new possibilities. AI can help manufacturers design innovative products, optimize supply chains, and personalize production based on real-time customer data. This data-driven approach fosters agility and allows manufacturers to adapt to changing market demands and consumer preferences.
Here are more use cases and advice about adopting Artificial Intelligence in manufacturing
#4 Computer Vision (CV)
Computer Vision, or Machine Vision, is a tool for analyzing dynamic human action in real-time. It observes, classifies, and responds to human events as they unfold. CV brings many benefits to the manufacturing industry, including time efficiency, reduced costs, and enhanced production accuracy. Let’s examine these benefits in more detail.
Firstly, with the help of Computer Vision, the automated system can operate faster and work around the clock if needed. So, the whole manufacturing process becomes more time-efficient.
Secondly, CV-based solutions allow manufacturing businesses to achieve higher accuracy within the accepted tolerance. In combination with CV algorithms, specific equipment enables near-perfect precision in the production process and quality control.
Thirdly, CV-driven solutions can help you to reduce not only labor costs (fewer staff members are needed to control the process) but also operational costs. As there is less waste due to less room for mistakes.
For instance, one of the clients that leveraged our Computer Vision development services was a German Global Fortune 100 multinational engineering and technology company. N-iX helped the client reduce operational overhead and warehouse downtime. This solution for cameras installed in warehouses allows automatic detection of arriving packages, scanning barcodes, and changing the delivery statuses of the boxes.
These Big Data trends are expected to evolve further and enable digital transformation in manufacturing. But how can manufacturers leverage Big Data? Let’s find out.
Big Data analytics use cases in manufacturing
Over the last few years, Big Data has become a game-changer in most industries. It helps healthcare, retail, finance, telecom, media, entertainment, and other companies make smarter decisions and predict business outcomes.
In manufacturing, however, the biggest value of Big Data is that it can not only forecast problems using data but also actually solve them. The time has come to shift from mere descriptive and predictive analytics to prescriptive analytics. It involves scenario planning, where companies plan activities based on data they have to avoid any untoward incident in the future. They can anticipate, for instance, a shortage of resources or a reduction in cash flow. Industrial manufacturing companies excel at different types of Big Data analysis techniques. According to the IBM report, they outpace their cross-industry peers in almost all analytics capabilities.
So, how can manufacturers benefit from Big Data in their businesses? What are the use cases for Big Data analytics in manufacturing?
Predictive maintenance
Many manufacturers say it is challenging to foresee when equipment needs service. Understanding the risks of lost production time due to a potential breakdown is difficult. Predictive maintenance, in turn, allows manufacturing businesses to reduce downtime and align maintenance schedules to create as little disruption as possible.
When the machine shuts down, professionals analyze why it has happened and collect data about this failure to prevent such damage in the future.
Price optimization
Big Data in manufacturing can also be used for price optimization when the price of the final product differs between suppliers and customers. When the data is collected and aggregated, and the data warehouse is ready, it is possible to run Data Science and Data Analytics to understand the price for each client.
Image recognition
Manufacturers can also leverage Big Data for image recognition at their manufacturing sites. Let’s say you need a spare part and have no idea what it is called, who the supplier is, how much it costs, etc. Searching for this information manually in the system takes a lot of time. Instead, you can take a photo of this product and upload it to the system, and it will give you all the information you need. This technology is based on the data lake, where the images of the products are collected.
Product line quality control
Thanks to Big Data, it is possible to identify quality issues in line production at the early stages. For instance, with the help of image recognition, manufacturers can check if the final look of the products corresponds to the required quality level. If the products have defects, they can be detected before they reach the customers.
Also, Big Data helps to reduce the number of no-fault-found (NFF) cases. An NFF is a unit removed from service following a complaint of the equipment's perceived fault. The unit is returned to service without repair if no anomaly is detected. The lower the number of such incidents, the more efficient the manufacturing process becomes.
Production forecasting
To optimize production, manufacturers must anticipate demand. Big Data in manufacturing comes in handy when collecting information about operations, businesses, and suppliers. It can help you better prepare for the future. Analyzing demand is crucial to avoid any shortage or excess of goods.
Supply chain
Big Data provides valuable insights at every stage in the logistics chain. In transportation, Big Data allows for real-time tracking of freights, weather, and road conditions. As a result, trucks can be diverted at any time on their way when a more cost-effective route is possible.
In warehousing, Big Data insights help businesses monitor or track the stock of supplies available in their warehouses.
Also, Big Data can help with product traceability in inventory management. It allows manufacturers to track the location of their goods throughout the logistics cycle.
Testing and simulation of new manufacturing processes
Both manufacturing processes and products can be tested before production. This is possible thanks to digital twins, VR environments, and manufacturing process simulations. Such environments and tools allow manufacturing businesses to optimize operations, detect issues, test settings, simulate scenarios, and predict performance.
How to effectively adopt Big Data in the manufacturing industry?
You should take three significant steps to adopt Big Data in manufacturing. They are:
1. Establishing transparent business KPIs and calculating ROI
Establishing clear KPIs and calculating ROI is vital. Suppose you need to validate your business's feasibility and profitability. In that case, you can undertake a Discovery Phase and, based on calculations for different scenarios, understand what benefits the implementation of Big Data can bring to your manufacturing process. The Product Discovery phase will provide all the deliverables required to efficiently kick off the implementation phase while addressing risks and optimizing costs.
2. Analyzing your manufacturing problems
It is important to get more details about your manufacturing problems and needs. You need to analyze the quality of your final product and the ways it can be improved. After that, you must consider all the pros and cons of adopting Big Data. Also, you must understand how applying Big Data in manufacturing can enhance the quality improvement process.
3. Ensuring an effective Big Data engineering process
In addition, you have to remember that the success of any Big Data analytics project heavily depends on the following aspects:
- finding top-notch Big Data developers who can help you on this challenging path;
- choosing the right data sources;
- building an orchestrated ecosystem of platforms that collect siloed data from various sources;
- cleaning, aggregating, and preprocessing manufacturing big data to make it fit a specific business use case;
- applying Data Science or Machine Learning/AI models;
- visualizing the insights.
Businesses that benefited from Big Data in manufacturing
- Fluke Corporation is a US-based manufacturer and distributor of electronic test tools and software for measuring and condition monitoring. N-iX has helped the client improve asset maintenance by arming maintenance teams with real-time asset information and tools to process it efficiently. We have ensured reactive and preventative equipment maintenance based on real-time asset data rather than a predefined calendar. As a result, the client has improved asset maintenance and significantly decreased maintenance costs.
- Another N-iX client (under NDA), an automotive technology company, needed a reliable partner for its digital transformation phase. The client wanted to digitize its manual processes. N-iX’s team has helped this client computerize the flow of warranty data between mechanics and vehicle manufacturers using a cloud-based application. With the help of the unified platform that stores all the data in one place, our client has improved data management efficiency.
- A Germany-based Global Fortune 100 multinational engineering and technology company has partnered with N-iX to redevelop its legacy platform. N-iX works on a computer-vision solution based on industrial optic sensors, lenses, and Nivida Jetson devices. This solution will allow this client to manage and track the goods.
Why choose N-iX as your Big Data services provider?
- N-iX boasts an internal pool of over 2,400 experts and a team of more than 200 data specialists.
- Our specialists have solid expertise in the most relevant tech stack for implementing Big Data in manufacturing, including BI, Data Science, AI/ML, Computer Vision, etc.
- N-iX partners with Fortune 500 companies to help them launch Big Data projects and migrate their Data to the cloud.
- Our Big Data experts have experience working with open-source Big Data technologies (both on-premise and cloud-based) such as Apache Spark, Hadoop, Kafka, Flink, Snowflake, Airflow, etc.
- N-iX complies with international regulations and security norms, including ISO 27001:2013, PCI DSS, ISO 9001:2015, GDPR, and HIPAA, so your sensitive data will always be safe.
References:
- The Forrester Tech Tide™: Smart Manufacturing, Q2 2020, Forrester Research, Inc., April 1, 2020
- Analytics: The real-world use of big data in manufacturing by IBM
- Consumer Review: Made-to-order: The rise of mass personalization by Deloitte
- Cloud Computing Trends: 2020 State of the Cloud Report by Flexera
- Big Data Analytics' Potential To Revolutionize Manufacturing Is Within Reach by Forbes
- Leading Through COVID-19: Post-Pandemic Opportunities for Manufacturing Industries by Gartner
- Effective ways to reduce manufacturing costs by BASM
- Big Data in Manufacturing industry size. Share & Industry analysis by Fortune Business Insights
Transform your manufacturing processes with AI: discover key use cases in the white paper
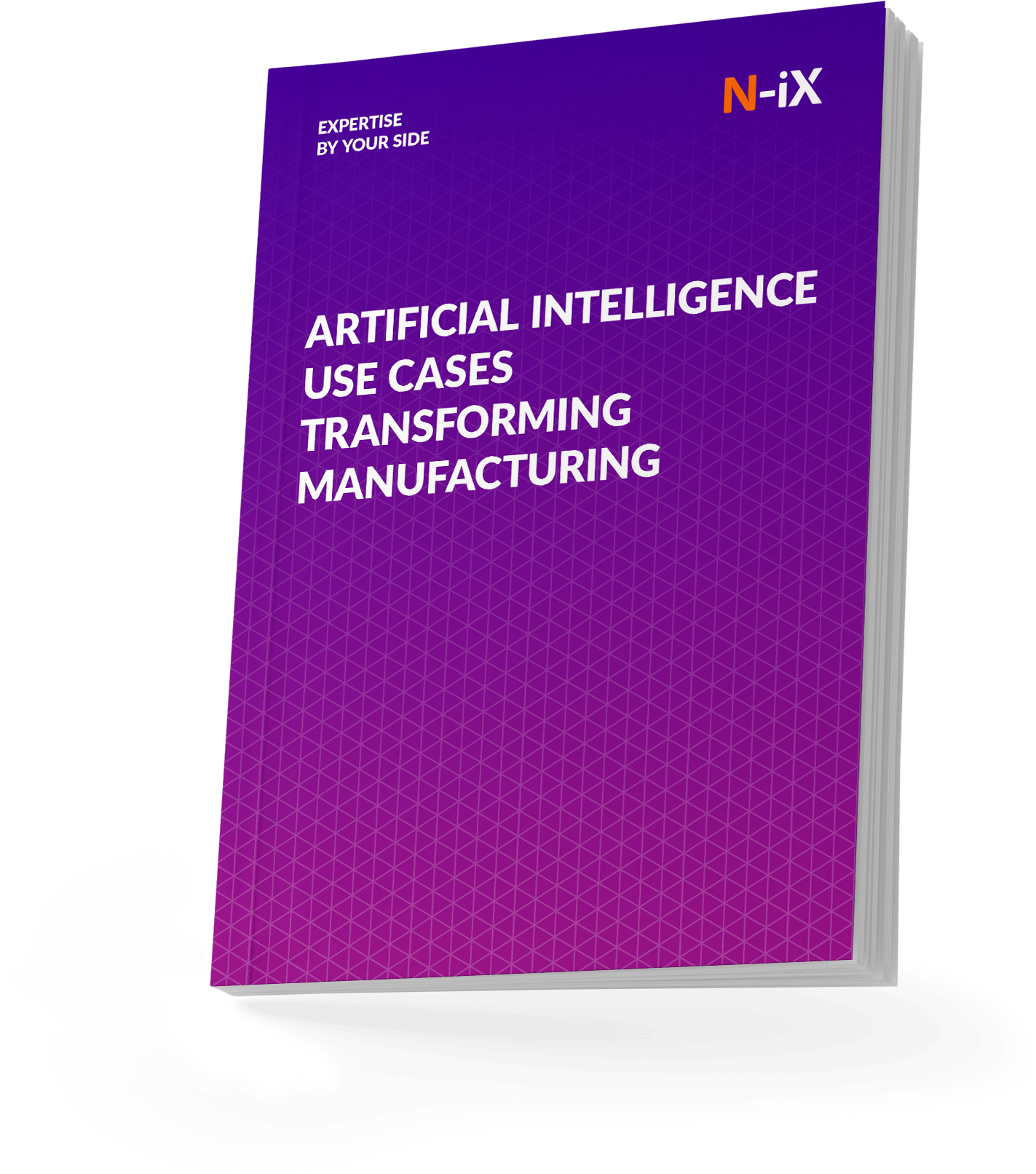
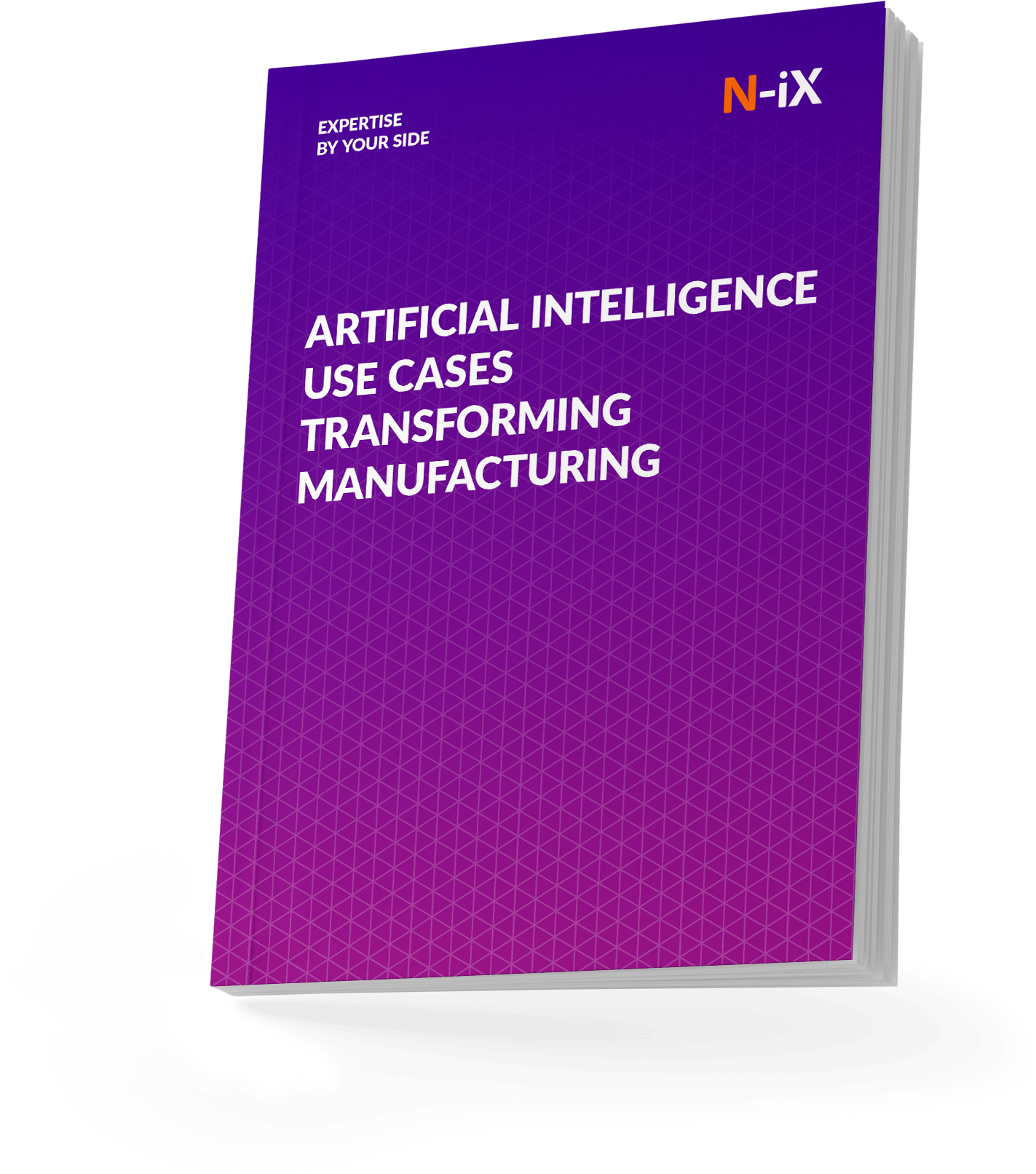
Success!
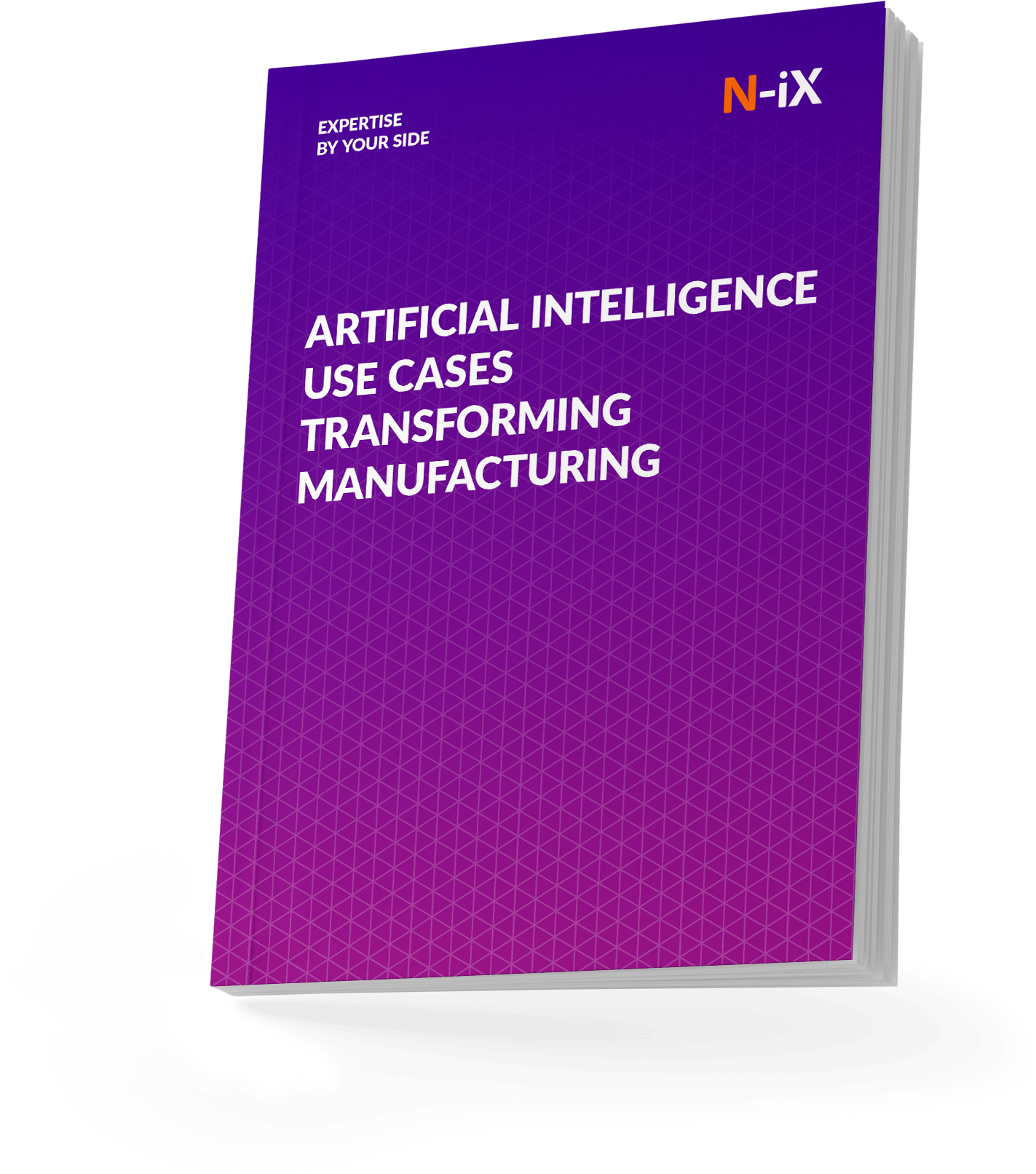
Have a question?
Speak to an expert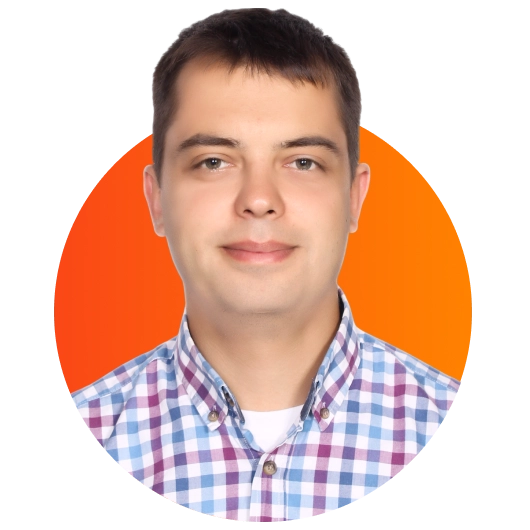