The manufacturing industry constantly seeks solutions to minimize machine downtime, optimize inventory management, and enhance operational efficiency to drive productivity. One of the technologies that can help satisfy these needs is the Internet of Things (IoT).
This network provides an organization with a constant data stream, allowing it to optimize the manufacturing processes and increase uptime. So, how does IoT help to achieve these results? Let us review the benefits of IoT in manufacturing, its use cases, and real examples of its applications.
Why should you use IoT in manufacturing?
Making precise decisions based on reliable data is one of the constituents of success for manufacturers. Combining IoT with such advanced technologies and approaches as Machine Learning, Big Data analytics, and automation makes real-time information available and helps improve the decision-making process.
- Machine Learning within IoT applications empowers systems to learn from data patterns, aiding in predictive maintenance schedules.
- Big Data analytics sifts through vast data sets, extracting valuable insights for enhancing production efficiency and decision-making.
- Automation technology, integrated with IoT, orchestrates seamless operations, optimizes production processes, and improves workplace safety.
The surge of IoT in manufacturing is fueled by its focus on predictive maintenance, heightened production efficiency, and streamlined infrastructure management. Combined with manufacturing software, it provides unparalleled visibility and control, promising to revolutionize the industry. In such a way, IoT fine-tunes production processes, minimizes downtime, and enables predictive maintenance.
What are the benefits of IoT in manufacturing?
Cost reduction
Manufacturing companies often look for ways to lower energy consumption, save budget on materials, and cover the losses associated with operational downtime. Here are the ways IoT helps to reduce expenses:
- Inventory and asset management optimization: Real-time insights from IoT sensors enhance inventory control.
- Downtime reduction: IoT-driven predictive maintenance detects equipment issues in advance, cutting down unplanned downtime and minimizing costly repairs.
- Energy efficiency: Energy usage monitoring identifies inefficiencies and enables real-time adjustments for reduced waste.
- Streamlining operations: Data-based insights optimize workflows, automate processes, and minimize errors.
IoT-powered automation reduces manual labor, optimizing resource allocation and minimizing errors. This cost-saving aspect and predictive maintenance significantly reduce operational costs and improve overall financial health.
Faster time to market
IoT significantly shortens the product journey from conception to market release in manufacturing through:
- Accelerated operations: IoT streamlines processes, enabling faster production cycles and efficient supply chain management. Real-time data optimization helps improve the timing of manufacturing processes, making products move faster from production to completion, ultimately reducing the time it takes to deliver products to customers.
- Improved connectivity: A seamless communication between employees and interconnected network components facilitates quicker decision-making, enhances collaboration, and ensures swift responses to market demands or alterations.
- Agile decision-making: With IoT-driven data analytics, companies swiftly adapt to market fluctuations. In such a way, companies can promptly adjust strategies or products, reducing time-to-market delays.
These IoT-enabled advantages accelerate product commercialization, reduce product cycle times, and result in substantial time savings.
Data-driven decision making
Manufacturers rely heavily on data, therefore an adept way of handling it enhances their business. IoT technology allows them to create an environment where rapid data distribution and insightful metrics drive faster, well-informed decision-making. Here’s how:
- Real-time data distribution: IoT sensors gather and swiftly disseminate critical data across robust networks via wireless or wired connectivity to a centralized system or cloud platform. This ensures real-time access to valuable insights throughout the manufacturing facility.
- Seamless information flow: With IoT, information flows rapidly across the manufacturing ecosystem, facilitating swift communication and informed decision-making at various operational levels.
- Performance insights: IoT provides valuable information for further system and device performance analytics. These insights empower managers to develop dashboard metrics continually, broadcast results swiftly, and facilitate prompt, data-driven decisions.
Merging IoT and big data analytics provides even more insights into production trends, supply chain efficiencies, and customer demands. This informed decision-making enhances resource allocation, inventory management, and product development, driving profitability.
You may also be interested in How reliable connectivity solutions define the future of IoT-powered smart manufacturing.
Mass customization
Customization is one of the trends in manufacturing that creates a demand for a profound expansion in stock-keeping units (SKUs). IoT emerges as the enabler for mass customization by:
- Enhanced personalization: IoT empowers buyers to personalize their choices efficiently by facilitating effortless component selection.
- Logistics adaptation: IoT enables suppliers and logistics providers to access precise component details and adjust schedules to align with orders swiftly.
IoT in manufacturing enables predictive forecasting that optimizes shop floor scheduling and streamlines data routing. This ensures a synchronized and responsive manufacturing ecosystem that efficiently meets mass customization demands.
Quality control and safety improvements
IoT sensors monitor and ensure product quality in real-time, reducing defects and minimizing rework. Automation also contributes to a safer work environment by handling repetitive or hazardous tasks. All of these can be achieved through:
- Risk detection: IoT systems identify and flag hazardous activities prone to causing injuries, contributing to preventive measures to mitigate potential risks.
- Safety solutions in hazardous environments: In potentially unsafe environments, IoT can continuously track environmental conditions, equipment performance, or the presence of potentially harmful elements. When certain parameters exceed safe thresholds or unusual activities are detected, IoT systems trigger immediate alerts or notifications to relevant personnel.
For instance, a security system that uses IoT in manufacturing facilities can monitor chemical storage areas. Any spillage or deviation from normal levels prompts instant alerts, preventing contamination and health hazards. Moreover, IoT-enabled emergency buttons or systems provide swift communication in crisis situations, ensuring immediate response and aid deployment in emergencies like accidents or injuries.
What are the ways to apply IoT?
Remote monitoring and control
IoT-driven remote monitoring empowers companies with real-time insights into industrial assets, ensuring efficient asset utilization and performance assessment. One of the examples of this approach is remote power consumption tracking throughout the production cycle. These possibilities allow for the creation of precise optimization strategies aimed at energy efficiency improvements and budget savings.
The ability to remotely monitor equipment health and swiftly deploy service interventions via IoT sensors significantly enhances operational efficiency and cost-effectiveness. Proactive alerts about potential machinery issues minimize downtime and maximize production uptime. Leveraging IoT-driven remote monitoring and swift interventions, manufacturers unlock opportunities to offer performance-based equipment services.
Digital twin technology
Adopting IoT-integrated digital twin technology revolutionizes how companies analyze their data. This advanced fusion of IoT, Cloud, Extended Reality (XR), and AI empowers businesses to create detailed digital replicas mirroring physical assets. A digital twin can be a powerful tool for different simulations, precise issue identification, and goal achievement without risking physical assets.
Companies gain a safe space for experimentation and analysis by replicating physical objects digitally. For instance, they might simulate the impact of adjusting machine settings to find the optimal configuration that maximizes output while minimizing energy consumption. This experimentation in the digital space allows them to fine-tune processes before implementing changes on the physical production line, thereby reducing risks, minimizing downtime, and enhancing overall efficiency.
Optimized logistics management
IoT transforms logistics by mitigating weather risks, curbing fraud, and bolstering asset supervision. With interlinked IoT applications spanning warehouses, fleet management, and cargo tracking, technology drives digital transformation.
For instance, at N-iX, we developed a solution for a manufacturing company to improve its fleet management and expand its customer base. Conducting a thorough feasibility analysis, our team developed an OEM-based Linux connectivity gateway and an Android-based app. The solutions facilitated smart fleet monitoring, operational efficiency, safety enhancements, and effective maintenance.
Enhanced manufacturing KPIs
IoT-integrated KPI dashboards empower data-driven decision-making, maintaining organizational focus and directing the company toward the optimal trajectory. For instance, let's consider a manufacturing plant aiming to optimize its Overall Equipment Efficiency (OEE) that assesses factory performance, availability, and quality.
For this purpose, a manufacturer can integrate IoT sensors into production machinery to capture real-time data on their equipment. This data will be displayed on the IoT-enabled KPI dashboard, offering comprehensive insights into production efficiency and identifying areas for improvement. With this information readily available, managers can swiftly address inefficiencies, reduce downtime, and enhance OEE.
Predictive maintenance
Downtime in manufacturing is a costly affair, causing disruptions and financial setbacks. Unexpected breakdowns can halt production, resulting in significant revenue loss and operational headaches.
Predictive maintenance powered by IoT leverages sensor data and AI algorithms to predict equipment failures before they occur. It detects subtle changes in machinery performance, enabling timely maintenance interventions.
As a result, manufacturers can schedule repairs during planned downtimes, avoiding unexpected breakdowns. This approach slashes downtime costs, ensures uninterrupted operations, and optimizes equipment lifespan.
Asset tracking
Asset tracking involves IoT technology to monitor and manage physical assets in manufacturing facilities. IoT sensors or Radio-Frequency Identification (RFID) tags integration helps manufacturers to accurately track the location, status, and usage patterns of machinery, tools, or inventory. This real-time visibility ensures that valuable assets are readily accessible, reducing search times and enhancing operational efficiency. Moreover, IoT-driven asset tracking helps prevent theft by providing continuous monitoring and immediate alerts in case of unauthorized movements or tampering.
More on the topic: Industrial IoT: best practices and key use cases
Navigate top 10 IoT challenges with our comprehensive guide!
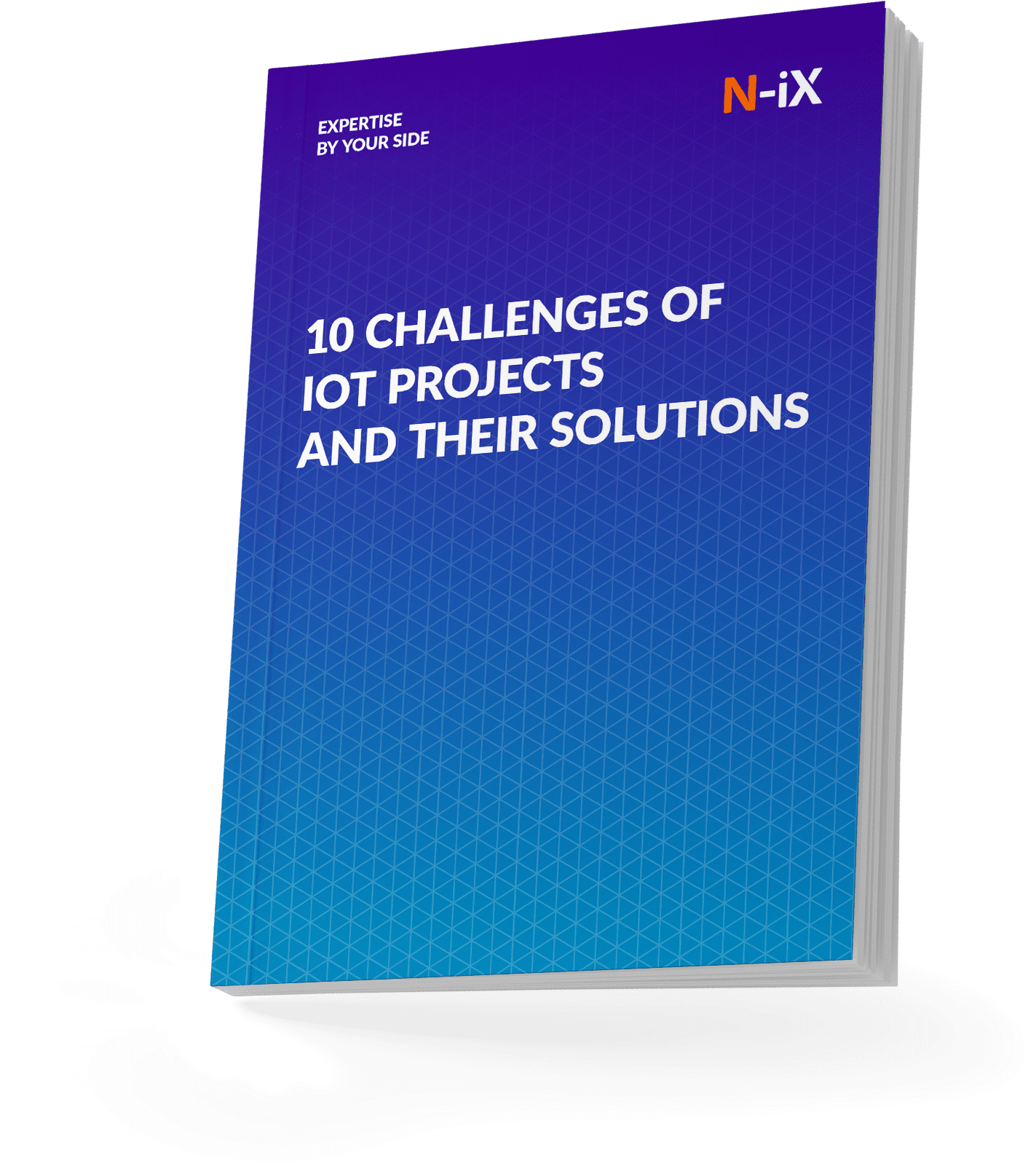
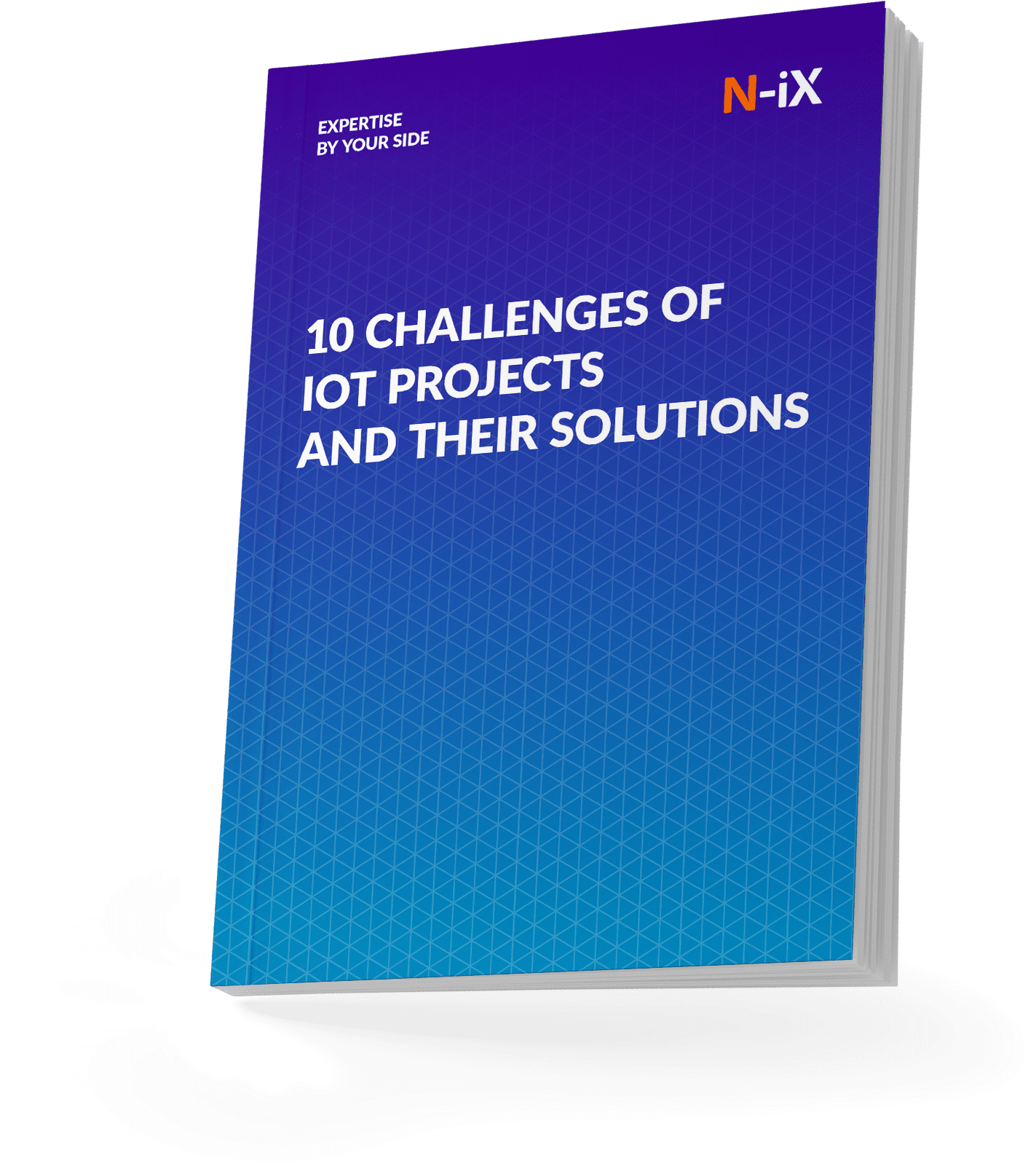
Success!
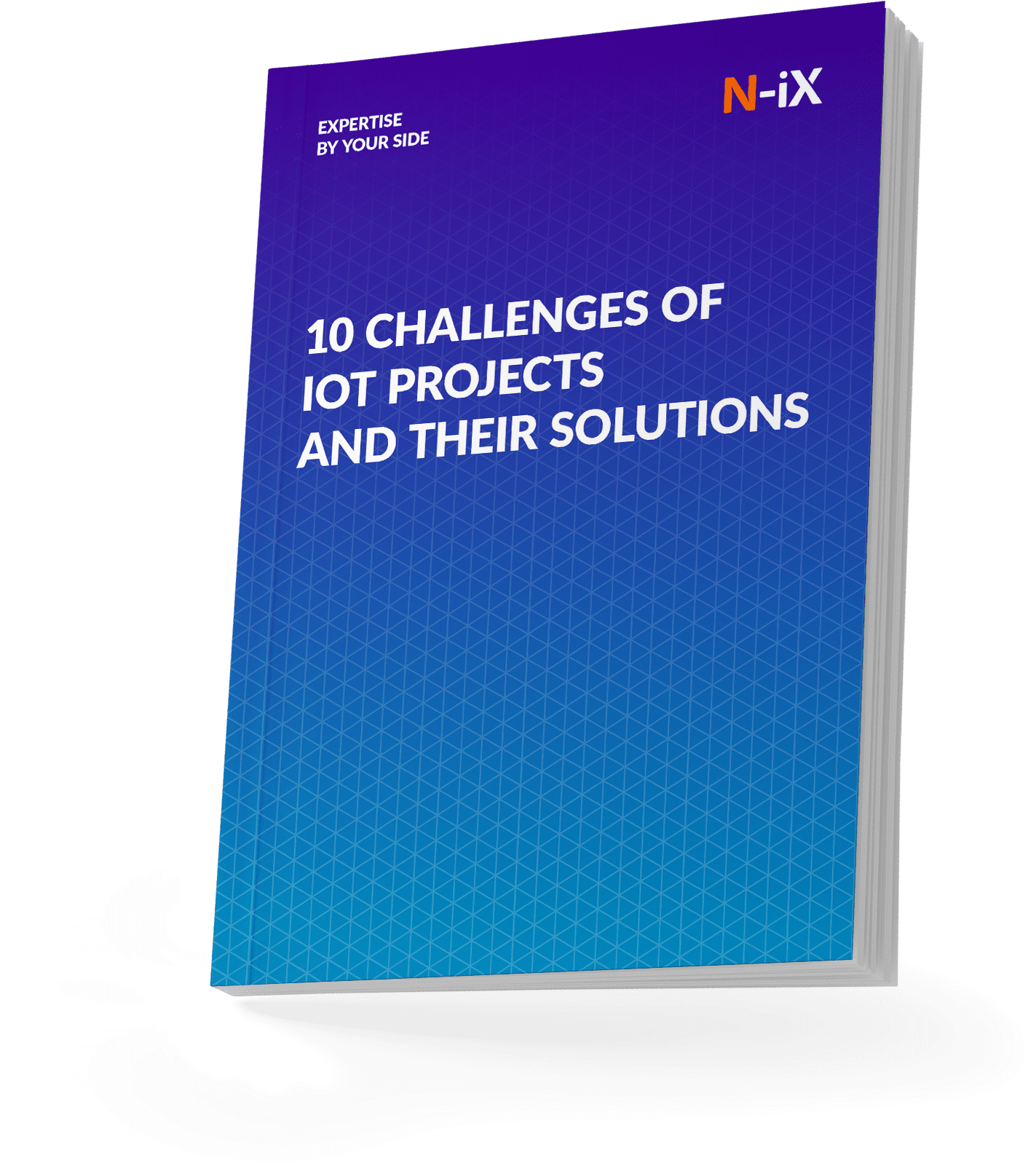
Wrapping up
In manufacturing, IoT solutions leverage such technologies as smart sensors, high-performance computing, and cloud platforms. These tools convert data into actionable insights, ensuring better decisions, safer operations, and efficient predictive analytics. Real-time data monitoring, smart asset management, and sensor integration prevent equipment damage, lower costs, and enhance product quality. This technological synergy empowers manufacturing with precision, cost-effectiveness, and superior product standards.
At N-iX, our deep expertise in IoT applications within manufacturing is proven by a wealth of experience and successful client collaborations. Over time, we have partnered with numerous industry leaders, harnessing the potential of IoT to drive transformative changes in their manufacturing landscapes. Step into the circle of our satisfied client community and let us empower your manufacturing journey with IoT-driven innovation.
Have a question?
Speak to an expert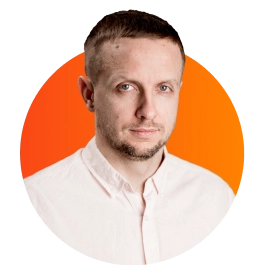