According to McKinsey, 23% of retail and consumer goods companies plan to invest over $500M in automation within five years, which is more than any other sector surveyed [1]. This statistic signals a clear shift in priorities as robotics in retail becomes a strategic necessity. Intelligent systems are already transforming core operations, from warehouse automation and shelf monitoring to cleaning and in-store fulfillment. Robotics supports faster execution, greater accuracy, and consistent customer experiences, which is especially helpful in managing rising labor costs and navigating omnichannel complexity.
However, successful implementation depends on the approach to process alignment and system coherence. It requires integration of robotics with store processes, data systems, and digital infrastructure. That is why partnering with a vendor that has strong expertise in robotics consulting and retail software development is essential. A trusted technology partner like N-iX will guide your project from feasibility assessment and early validation to full operational rollout and sustained performance across the retail environment.
What can you automate with robotics in the retail industry?
Retailers today operate under immense pressure to deliver faster service, leaner operations, and personalized experiences, all while managing labor shortages and growing cost volatility. Robotics has transitioned from a futuristic concept to a tactical asset that enables retailers to scale without overextending their workforce or infrastructure. Below are the most business-critical use cases that illustrate why robotics in retail is becoming an operational necessity.
Customer service and information
Physical stores remain strategically important, but they are increasingly expected to operate with fewer staff while still delivering high-quality service. Robotics in retail is equipped with conversational interfaces and multilingual support to assist by guiding customers to products, answering questions, and offering personalized suggestions. In large-format retail, robots also manage queue flow and reduce customer frustration. This approach addresses rising service expectations with predictable, scalable automation that maintains consistent performance.
Warehousing and back-end operations
Behind every seamless retail experience lies a fulfillment engine under constant strain. Labor turnover in warehouses remains high, and rising wage pressures limit scalability. Retailers employing autonomous mobile robots and robotic arms for picking, sorting, and inventory transport can sustain peak throughput even with constrained staff. These systems enhance speed, accuracy, and consistency.
As demand variability grows, the ability to scale operational capacity without hiring or retraining becomes a competitive differentiator. Therefore, 80% of companies surveyed by McKinsey have either adopted or are likely to adopt automation for routine tasks such as palletizing and depalletizing [2]. Even though the survey participants were manufacturing companies, the challenges they address with robotics are similar to those experienced by retail warehouses, distribution centers, click-and-collect fulfillment hubs, grocery stores, and big-box retailers.
Inventory management and shelf monitoring
Inventory inaccuracies, such as empty shelves, misplaced items, and pricing errors, are expensive and persistent problems in retail, leading to lost sales, poor replenishment decisions, and a decline in customer trust. Robotics in retail mitigates this risk by autonomously scanning shelves, identifying stockouts, and flagging pricing errors in real time. That is why inventory management robots are the most widespread type of robot by application, holding 31,7% of market share in 2025 [3].
Using sensor fusion and advanced navigation, these robots adapt to dynamic foot traffic and operate safely alongside shoppers. Real-time detection of stockouts and pricing discrepancies eliminates the need for manual audits, ensuring that merchandising plans are executed accurately and efficiently. These capabilities result in higher on-shelf availability, reduced labor costs, and improved sales conversion.
Click-and-collect
Click-and-collect has become a standard offering in omnichannel retail, allowing customers to make an online purchase and pick it up at a physical location. Yet fulfilling these orders quickly and accurately often presents logistical challenges. Robots that handle in-store picking and manage collection points enable faster turnaround and reduce friction for store staff. Especially during high-traffic seasons, robotic assistance ensures that order fulfillment doesn't impede front-of-house operations or compromise customer satisfaction. For retailers, this translates to fewer errors, lower operating costs, and improved margins on each order fulfilled.
Cleaning and maintenance
Hygiene expectations in retail have permanently increased since the pandemic. Dedicating staff to routine cleaning and equipment checks is inefficient, particularly when skilled labor is scarce. Robotics in retail, which cleans floors, organizes misplaced items, or diagnoses technical issues, allows employees to focus on higher-value tasks while ensuring operational compliance. These robots transform maintenance from a reactive cost center into a proactive function, helping retailers avoid equipment failures, reputational damage, or safety violations.
Last-mile delivery
The last mile often constitutes the most expensive segment of the fulfillment process, accounting for 53% of total delivery costs. Robotics alleviates this burden through autonomous ground vehicles and drones that integrate with delivery platforms and point-of-sale systems. For retailers, these robots open up new service models, such as same-day delivery from local stores, without relying on third-party fleets. Greater control over last-mile logistics enhances customer experience and fosters higher retention.
Supply chain automation
Retailers with complex distribution networks face escalating demands for transparency, speed, and flexibility. Robotics in retail extends beyond task execution, as autonomous systems use predictive algorithms to optimize sorting, routing, and fulfillment. These platforms integrate with warehouse and transportation management systems to maintain real-time visibility across the supply chain. IoT in retail plays a critical role in enabling robotics platforms to access real-time logistics data, optimize routing, and improve responsiveness to shifting demand patterns. The business value lies in more accurate demand forecasting, accelerated fulfillment cycles, and tighter synchronization between inventory flow and real-time customer needs.
Boost operational excellence—get your ultimate guide to robotics in logistics today!
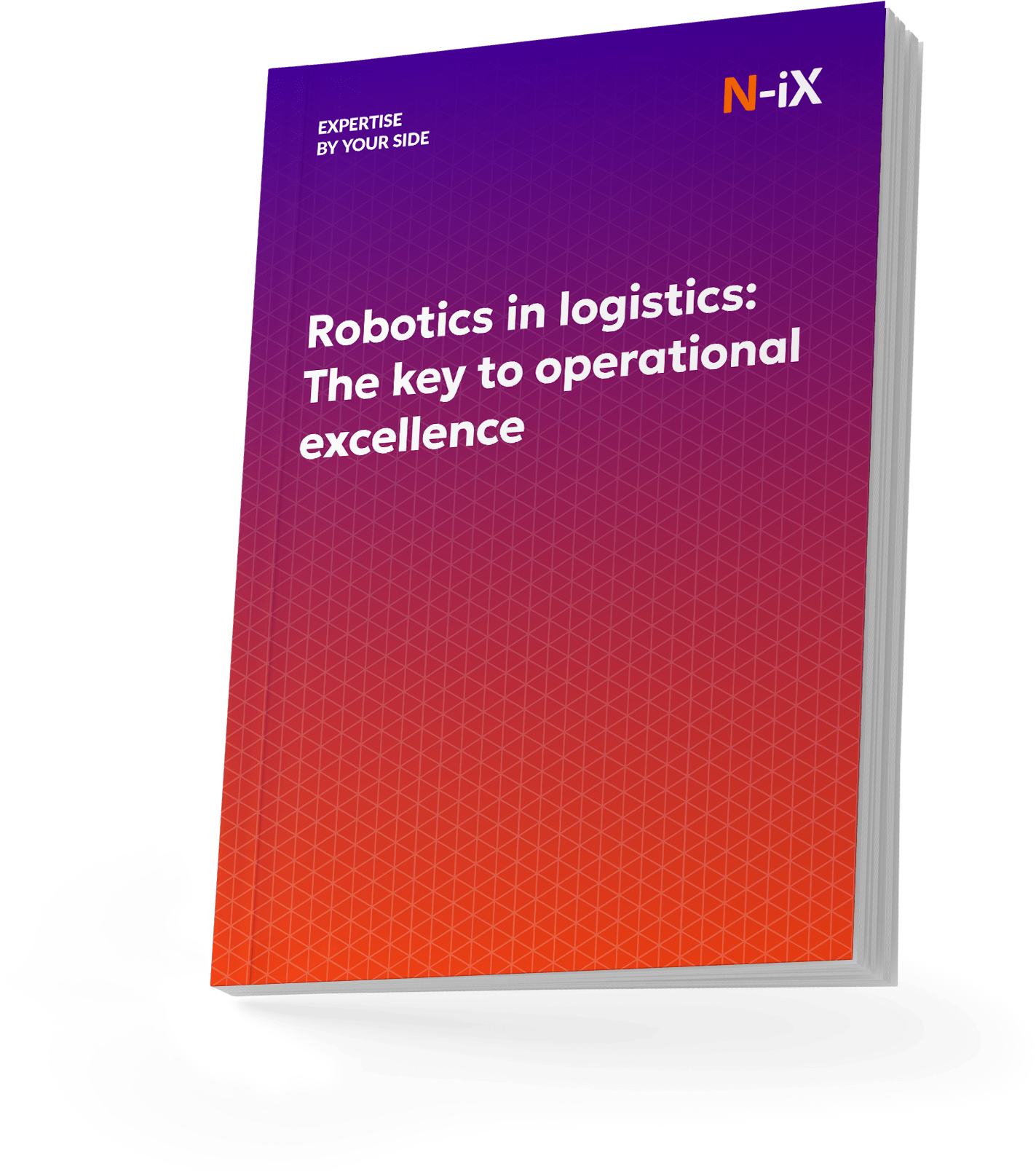
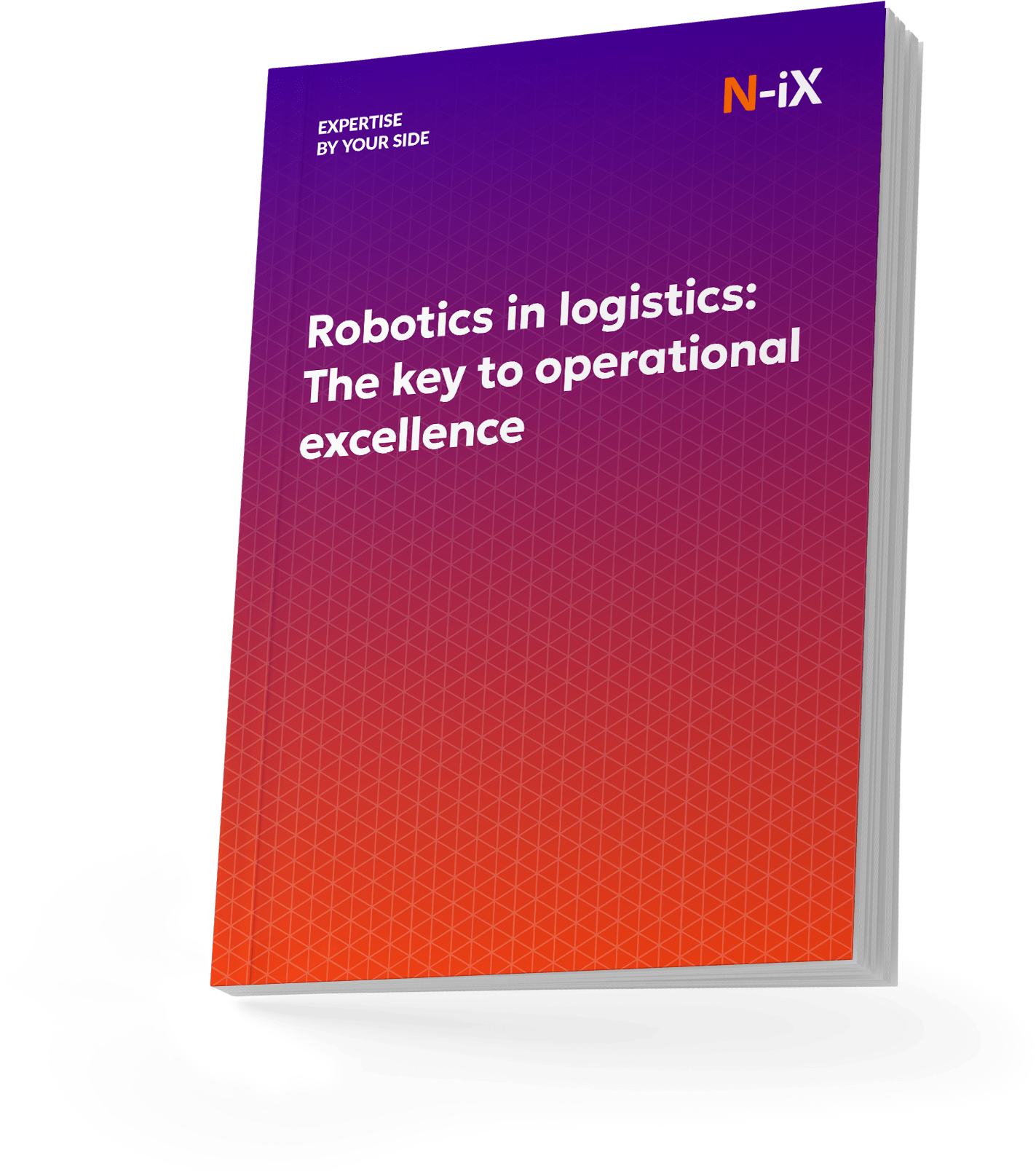
Success!
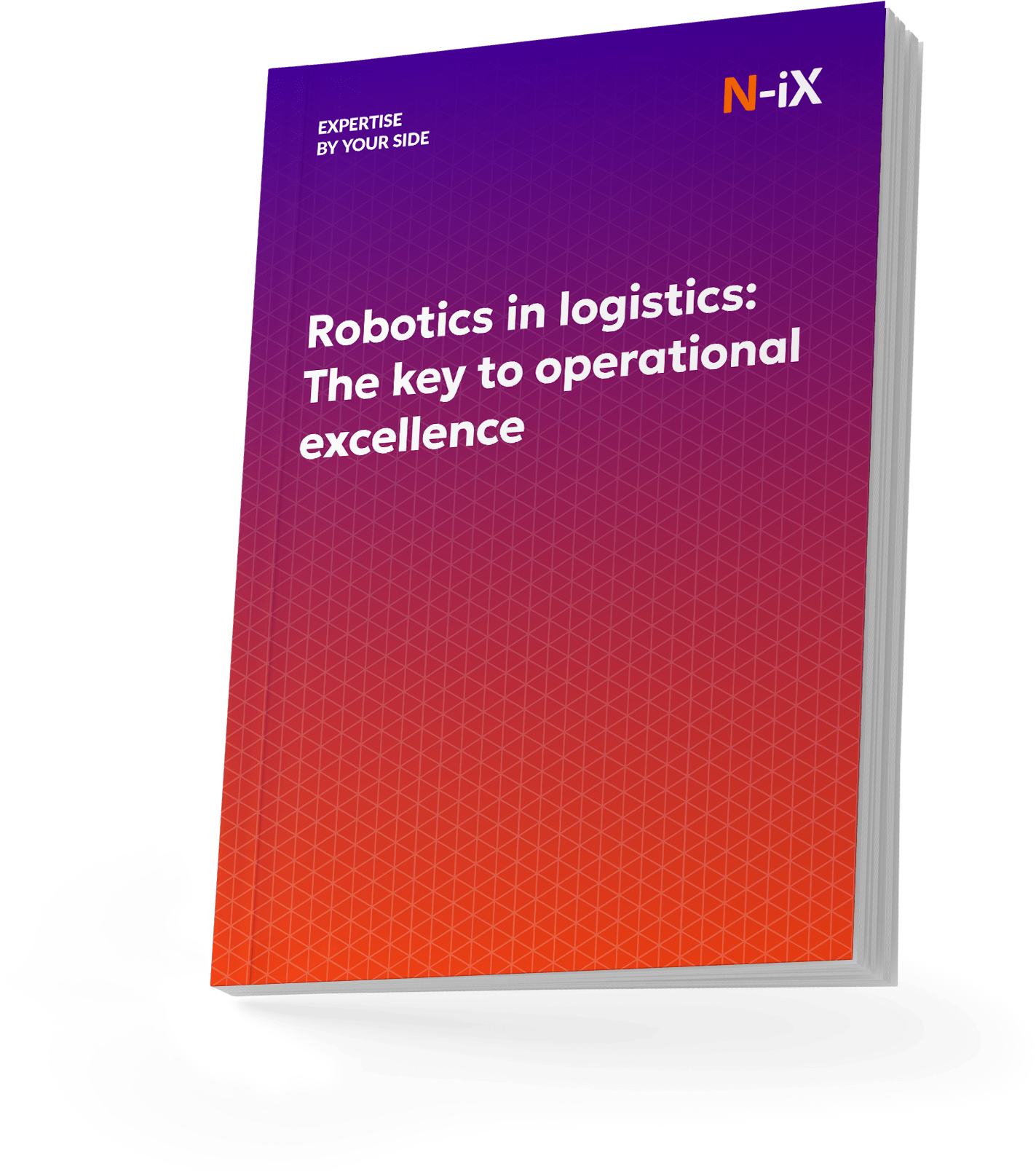
Robotics-as-a-Service (RaaS)
Historically, the high cost of robotics adoption posed a barrier for many retailers. Robotics-as-a-Service (RaaS) mitigates this challenge by shifting from capital expenditure to a subscription-based model. Retailers can now rent, pilot, and scale robotic solutions on demand, without significant upfront investment. Combined with modular hardware and software, a single robot can be reconfigured for various tasks as business needs evolve. This model democratizes access to automation, enabling mid-sized retailers to adopt robotics and allowing enterprise retailers to scale rapidly across regions.
Key challenges in retail robotics adoption and how N-iX solves them
While the potential of robotics in retail is substantial, successful adoption depends on carefully navigating technical, operational, and human factors. Addressing these challenges early enables smoother integration and long-term scalability. N-iX brings both domain knowledge and technical depth to help retailers overcome these barriers and capture business value from retail automation.
High implementation costs
Retail robotics involves significant upfront investments in hardware, system integration, and technical infrastructure. The return on investment is often dependent on operational scale and the maturity of digital processes. For retailers with fragmented legacy systems or limited robotics experience, financial risk can hinder adoption or delay deployment.
Solution by N-iX: N-iX helps organizations de-risk robotics investments by delivering structured support from feasibility assessment to on-site deployment. Our approach begins with technical and financial due diligence to assess the viability and scalability of robotics within the client's specific environment. Through partnerships with Amazon and MathWorks, we leverage tools like MATLAB, Simulink, and model-based design to develop and adapt control software across multiple robot types rapidly. We provide early-stage proof-of-concept pilots to validate outcomes before rolling out on a large scale, ensuring cost alignment with value delivery.
Reliability and safety
In customer-facing environments, robotic systems must perform consistently under unpredictable conditions, handling edge cases without compromising safety. Compliance with machine safety and human interaction standards is non-negotiable, especially in high-traffic, public-facing settings.
Solution by N-iX: N-iX applies a certified safety-first engineering process to ensure the reliability and compliance of robotics solutions. We design and test systems according to global safety standards, including ISO/TS 15066 for collaborative robots, ISO 13849-1 for machine control systems, and ISO/PAS 21448 for the safety of intended functionality. Our frameworks also integrate AI risk management (ISO/IEC 23894) and GDPR-compliant data handling, ensuring safe, transparent, and regulation-aligned deployment across store environments.
Integration with existing processes and systems
Legacy IT infrastructure and siloed ERP platforms often lack the flexibility needed to support robotics. Poor integration can result in fragmented workflows, increased maintenance overhead, and loss of data continuity across systems.
Solution by N-iX: We begin by conducting a detailed analysis of the client’s current systems, identifying integration gaps and process bottlenecks. Our engineering teams develop middleware and custom APIs that allow robotics systems to interface smoothly with legacy environments. Robots are integrated into existing workflows incrementally, starting with repetitive and high-friction tasks. This approach ensures continuity, reduces implementation risk, and enables measurable efficiency gains over time.
Workforce adaptation
Transitioning from manual operations to tech-enabled environments can disrupt established roles. Without proper planning, robotics adoption may face internal resistance or result in workforce displacement without long-term upskilling strategies.
Solution by N-iX: We help retailers build transformation roadmaps that include people alongside technology. Robotic systems are introduced gradually, and employees who previously performed the tasks are involved in teaching and supervising robotic behaviors during the early phases. Over time, this hands-on experience prepares them to take on higher-value, decision-making, and supervisory roles—elevating human contribution rather than replacing it.
For instance, in one of our projects, we implemented robotics to automate a previously manual process. The same professionals who had performed the task manually were involved in teaching the process to cobots and later took on supervisory roles to oversee their performance. This transition not only ensured a smooth knowledge transfer but also supported workforce upskilling and professional growth.
Ensuring customer acceptance
Not all shoppers are immediately comfortable interacting with robots in public settings. Perceptions of complexity, impersonality, or lack of transparency can negatively impact the customer experience and brand reputation.
Solution by N-iX: N-iX designs robotics systems with human-centered interaction in mind. Our solutions prioritize approachable form factors, transparent workflows, and intuitive user interfaces. We incorporate features such as visible task indicators, human override options, and responsive support escalation (seamless connection to human staff when needed). Pilot deployments include signage, guidance, and interaction training to gradually build trust. The result is a system that feels helpful but not intrusive. In this way, our solutions deliver value without disrupting the shopping journey.
Wrap up
Retailers embracing robotics are gaining a decisive advantage in precision, speed, and operational resilience. As demand for real-time fulfillment, intelligent inventory control, and seamless customer service continues to grow, automation is becoming a core driver of performance. Robotics in retail enables measurable gains in efficiency, reduces labor dependency, and supports higher service quality on a larger scale. It is a strategic investment with a direct impact on competitiveness and profitability.
N-iX is a reliable partner for companies seeking to implement and scale robotics in the retail industry. With over 200 experts in data and AI among the team of 2,400 specialists, we provide end-to-end support across the entire robotics lifecycle. Our team delivers expertise in control systems, simulation, system integration, and real-time analytics. Through strong partnerships with AWS, MathWorks, and other technology leaders, and with deep experience in model-based design using tools like MATLAB and Simulink, N-iX helps retailers turn complex automation initiatives into scalable, secure, and high-impact retail robotics solutions.
References
- McKinsey - Unlocking the industrial potential of robotics and automation
- McKinsey - Can automation help with talent challenges
- Coherent Market Insights - Retail robots market size and trends
Have a question?
Speak to an expert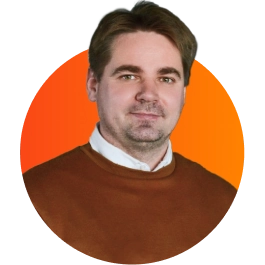