In this day and age, automobiles and other vehicles depend on tech—resilient custom software is no less important than the hardware. Modern cars rely on millions of lines of code to run. Just to show you the scale of things, a car requires more code and a more complex software system than an average passenger plane (according to NXP). These trends will only continue to grow with an increasing demand for connectivity, autonomy, and alternative energy.
And while a car itself is a complex embedded system with tons of components, we will cover only one of them in this article: an automotive battery management system. An effective automotive BMS solution takes a lot of time, tons of expertise, and an in-depth-understanding of both requirements, hardware, and software. Why do companies need battery management solutions? Is there an effective way to approach this process? How can a great automotive BMS improve the overall approach to production?
Why is BMS needed?
While Lithium batteries are nothing new in the manufacturing of small electronic devices (such as mobile phones), it is a relatively modern technology for the automotive industry. Li-ion batteries require complex monitoring and supervision systems, as in a large group of cells and constantly changing environment such batteries tend to be unstable. Among the most common challenges most manufacturers face are:
- The need for a deep understanding of how the BMS in automotive works and how the controller is supposed to be designed, and what algorithms should be used;
- High margin of human error and lack of automation;
- The demand for Aautomotive SPICE-compliance test reports and documentation for further certification.
To address these issues, the industry refers to BMS solutions to monitor and control batteries in cars.
3 major functions of a BMS in the automotive industry
No one wants a battery that can explode or act up. Companies that produce batteries for electric vehicles, want an automotive BMS to serve these major tasks:
- Battery protection to prevent operations outside its safe operating range;
- Battery monitoring to calculate the state of charge (SoC) and the state of health (SoH) while the battery is being charged and discharged;
- Battery optimization (via cell balancing) to improve the battery life and capacity, thus increasing the driving range of hybrids, plug-ins, and fully electric vehicles.
But how can the company design and develop a battery management system that can be effectively used in the automotive business vertical?
Traditional vs model-based development: which one suits your business more
There are two ways to approach the development of battery management systems for the automotive industry. The first one is the traditional style. You take your requirements, transform them into a technical specification, then an engineer codes it, and this code is later tested on a physical device. And while this approach has been working for almost two decades, more and more businesses rely on an alternative approach.
On the contrary, the model-based approach allows companies to have flexible and scalable development, with automated code generation and little human intervention. Let’s explore the reasons why the model-based process makes an excellent choice for OEMs and Tier 1 companies.
Model-based as a new way to approach battery management systems in automotive
The idea behind this concept is to apply mathematical and computer analysis methods to design and develop individual cells and batteries.
How does the software component of automotive BMS operate in a model-based approach?
Let us begin with a simplified schema of the process:
- First of all, engineers gather requirements from all available sources/channels and turned them into executable specifications;
- Then, these specifications are transformed into code within the Simulink model;
- Once the model is designed and working properly, it is generated via C/C++ code;
- The model undergoes a series of test and verification procedures;
- And after that, it is tested on a physical target device.
A typical model of a BMS designed in Simulink covers:
- The design of batteries;
- Algorithms to check the major parameters of the current battery performance;
- Potential scaling and extension opportunities;
- Impedance calculation for health evaluation of a system (as a whole and individual cells);
- Ability to control and ‘turn off’ cells that are not working properly.
Overall, designing an automotive battery management system in Simulink has multiple benefits, namely:
- Inclosed author and requirements management;
- Early verification to find defects;
- Manual and automated verification of implementation/code/model/etc.;
- Workflow that conforms to safety standards;
- Static сode review.
Here at N-iX, we offer full-cycle development, based on both traditional and model-based approaches. It allows us to cover every stage of the process: from the analysis of requirements to the documentation you will need for certification. However, we recommend our clients go for a model-based approach. Our engineers create a complex ecosystem and a single, automotive-certified development space that provides a solid ground for functional safety, test- and documentation traceability, and reduction of human involvement.
However, these are not the only advantages of creating battery management systems via model-based design.
Easier compliance with international standards and certifications
Any reputable automotive company (whether it’s an OEM or a vendor that provides software components) should be compliant or at least well-versed in the industry regulations, such as Automotive SPICE, ISO 9001, ISO/SAE 21434:2021, ISO 26262, and ISO/IEC 33020:2019.
Not only are such compliances necessary for further certification, but it is a critical success factor for the design and implementation of the system in general. When a company has an in-depth understanding of the Aautomotive SPICE framework and all the ISO standards required by the automotive industry, it can deliver high-quality products that will be effective and certifiable.
Read more about full-cycle automotive testing services.
Our featured expertise in BMS for the automotive industry
- We have designed a Simulink Model of the Li-Ion Battery cell that has been used as a test target and debug tool for developing the EV charging system. We did more than 1,000 tests showing a deviation of less than 2.3% from the benchmark battery cell. That gives us the possibility to use the model as a validation tool.
- N-iX specialists worked on predicting the State of Life (SoL) of a Lithium-based battery pack. As a result, we created an algorithm that can estimate the Live terms of the Battery Pack. We optimized the algorithm in Python and implemented it using C. This code can be run as an AUTOSAR SWC. Also, we made it compact, safe (ISO 26262), and secure (ISO 21434). Our specialists tested it and prepared all the necessary documentation according to ISO/IEC 29119.
- Our engineers worked for the biggest Scandinavian OEMs and a few other European Tier 1 and Tier 2 companies. Some of our applications also work as Libraries and SWCs on products of Asian OEMs.
Why should you choose N-iX as your automotive BMS partner?
N-iX delivers projects to OEMs, Tier 1, and Tier 2 automotive companies, providing a full cycle of development services: from system analysis and requirements preparation–all the way to qualification support. The company adheres to the highest standards and complies with the required regulations of the automotive industry.
Have a question?
Speak to an expert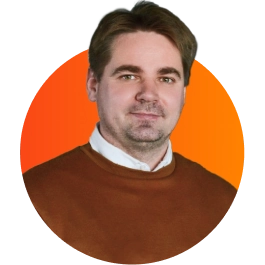